Главная :: Акустика:: Профессиональные АС своими руками.2006-06-28
Цель данного опуса - поделиться собственным опытом создания акустических систем (АС) профессионального типа. Замечу, что изложенное не является догмой, вполне возможны иные варианты и решения. Намеренно не рассматриваю вопросы проектирования, поскольку им посвящены целые книги, а сам не являюсь крупным специалистом в данной области.
Замечено, что кроме высокой чувствительности, надежности и приемлемого качества звучания, профессиональная АС должна быть достаточно компактной и легкой, удобной в транспортировке, стойкой к внешним воздействиям (влага, механические удары, пыль и пр.), травмобезопасной, не повреждать соприкасаемые с нею поверхности, иметь хороший внешний вид.
Компромиссов при создании АС будет предостаточно, например, низкочастотные звенья имеют значительный объем и габариты (зависит от типа оформления, применяемой динамической головки, требуемой АЧХ и пр.) и безнаказанно уменьшать их нельзя, поскольку снижается отдача на самых низких частотах. Остается только некоторая свобода выбора формы корпуса. Так, корпус можно сделать узким, неглубоким, но высоким, он будет занимать меньшую площадь. Как правило, ширина корпуса (при оформлении типа закрытый ящик, фазоинвертор) определяется диаметром наибольшего применяемого динамика.
Важной задачей является защита АС от разного рода внешних воздействий. Следует защищать от механических повреждений динамики и некоторые уязвимые места корпуса, такие как углы, дно, входные разъемы (клеммы). Защита динамика осуществляется углублением передней панели внутрь корпуса и применением металлической сетки, которая может закрывать всю переднюю панель. Углы защищаются так называемыми угловыми набойками (металлическими или пластиковыми), они же обеспечивают некоторую травмобезопасность. Защита разъемов и клемм обеспечивается конструкцией самого терминала. Осталось защитить дно (и поверхность, на которой АС будет установлена), для чего используются резиновые ножки, именно они, а не сверхаудиофильные шипы. Травмы ног и поцарапанный пол вовсе ни к чему.
Удобство транспортировки достигается установкой металлических или пластиковых ручек, конструкция последних такова, что они \"спрятаны\" внутрь корпуса.
Для придания законченного внешнего вида используют лакокрасочные покрытия, ударопрочные пластики, специальную ворсистую ткань (карпет). В процессе транспортировки всегда существует вероятность нанесения удара по панелям корпуса, и это следует учитывать при выборе покрытий. В этом плане наилучшим считаю карпет, поскольку на нем практически не остается следов удара, но это не значит, что его нельзя повредить, всему есть предел. Карпет достаточно просто клеится (даже при отсутствии опыта получается хороший результат, огрехи очень хорошо скрываются ворсом), скрывает значительные неровности поверхности корпуса. Также отпадает необходимость герметизировать устанавливаемые в панели элементы (динамик, терминалы, ручки). Замеченные недостатки - немного впитывает пыль, плохо переживает пролитые на него пахнущие и имеющие цвет жидкости. Не стоит выбирать черный карпет, он хорошо смотрится, но так же хорошо пачкается и на нем видна пыль.
Не исключена возможность попадания АС под дождь или проливание на нее жидкости, так что следует принять это к сведению. Сказанное вовсе не значит, что акустика должна работать под проливным дождем, но разлитое на нее пиво не должно нанести существенного вреда. Считаю, что достаточно покрыть одним-двумя слоями лака чувствительные к влаге поверхности корпуса.
Некоторые варианты конструкций АС можно посмотреть здесь: http://members.tripod.com/~sakevich/.
О материалах. При выборе материала корпуса АС необходимо учитывать, что он должен быть достаточно прочным, и при этом умеренно тяжелым, желательно стойким к влаге. Важным также является высокое внутреннее поглощение колебаний в материале (он не должен быть \"звонким\").
Для изготовления корпусов АС в основном используются древесностружечные, древесноволокнистые плиты (ДСП, ДВП), фанера. Наиболее дешевой является ДСП, покупка и порезка комплекта панелей из плиты толщиной 18 мм для двух АС в мебельной фирме обойдется в 10-12 у.е. ДСП имеет хорошие показатели внутреннего поглощения, достаточно прочна и легка, хорошо обрабатывается. Из недостатков склонность к расслоению и выкрашиванию кромок листа, требует влагозащиты. Фанера более прочная, что позволяет уменьшать толщину стенок ящика, но одновременно более \"звонкая\" и значительно (в 2-3 раза) дороже ДСП и также должна защищаться от влаги. Влагостойкая фанера еще в несколько раз дороже. Если предполагаются жесткие условия эксплуатации, то следует предпочесть фанеру.
При покупке материалов, особенно ДСП следует обратить внимание на их качество, поскольку выпускается нескольких сортов, хранятся в разных условиях и т.п.. Порезку имеет смысл производить там же, у продавца. Незначительные финансовые затраты (около 0,25-0,3 у.е за погонный метр) полностью окупаются высокой точностью изготовления деталей, что очень облегчает и упрощает сборку корпуса.
Также понадобиться деревянный брус сечением 25х25 и 25х50.
О инструменте. Для работ нам понадобиться следующее: электродрель, набор сверл (диаметром до 10 мм), острый нож, пила по дереву или электролобзик, отвертка, молоток, малярные кисти, линейка, уголок, циркуль, карандаш. При отсутствии электролобзика, для вырезания небольших отверстий (под ручки, терминалы) может пригодится полотно для ножовки по металлу, нужно только сделать подобие ручки, обернув часть полотна изолентой, тканью, пр.. Работать такой \"пилой\" следует осторожно, с небольшим (3-5 см) ходом, полотно хрупкое, можно пораниться.
О конструкции. На дно корпуса \"поставлены\" боковые панели, их в свою очередь \"накрывает\" верхняя панель. Задняя панель \"накрывает\" торцы боковых и верхней/нижней панелей (фрагмент стыка со стороны задней панели, без нее самой, показан на фото 1). Передняя панель утоплена вглубь корпуса на 40 мм для предотвращения повреждения динамика (динамик и защитная сетка должны полностью спрятаться). Такое построение корпуса позволяет минимизировать количество точек, имеющих нагрузку на срез (разрыв).
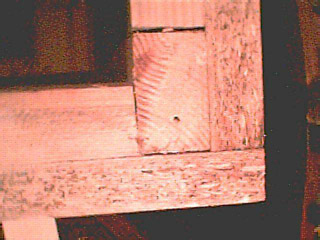
Фото 1.
Стенки корпуса соединяются при помощи шурупов, клея ПВА и деревянных (сосновых) брусков сечением 25х25 мм. Сборка осуществляется следующим образом.
Закрепляем по 4 бруска на каждой боковой панели, причем брусок, предназначенный для крепления передней панели должен отстоять от края на желаемую глубину посадки динамика плюс толщину ДСП. Остальные 3 бруска должны образовывать совместно с торцами боковой панели ровные поверхности (можно незначительно, на 0,5 мм, отступить от края панели, что позволит соединяемым панелям примыкать непосредственно друг к другу и обеспечить таким образом лучшую герметичность соединения). На фото 2 показан фрагмент стыка со стороны передней панели.
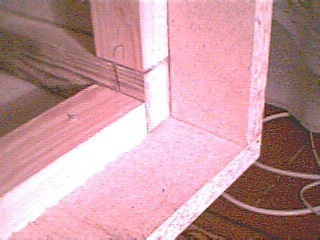
Фото 2.
Если фазоинвертор будет являться частью корпуса, то нижний стык должен выглядеть так, как показано на фото 3 (к его конструкции еще вернемся):

Фото 3. На дно корпуса брусок не прикручиваем, нижняя панель будет частью трубы фазоинвертора.
Расстояние между шурупами в пределах 100-130 мм, от торца бруска нужно отступать не менее, чем на 25 мм, иначе он может расколоться от вворачиваемого шурупа. Шурупы следует использовать специально предназначенные для дерева (с крупной "резьбой", фото 4) размер 3,5х45.
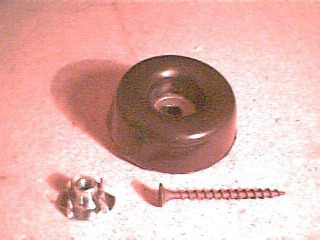
Фото 4. Так выглядят шуруп по дереву, "вбиваемая" гайка. На заднем плане - резинопластиковая ножка.
В панелях под шурупы обязательно сверлим отверстия и зенкуем их, чтобы шурупы не выступали над поверхностью. В брусках тоже желательно сверлить отверстия (малого диаметра, около 1,5 мм), поскольку древесина бывает очень плотной и шуруп вворачивается со значительным усилием. Кроме того, уменьшается опасность расколоть брусок.
Количество наносимого клея должно быть таким, чтобы после стягивания шурупами клей выступил, но не обтекал. Так обеспечивается герметичность соединения и экономное использование клея. Не допускайте попадания клея ПВА на внешние поверхности, он плохо уживается с масляными лаками.
Соединяем боковые панели с верхней и нижней, нарезаем и закрепляем еще 4 (3, если фазоинвертор будет частью корпуса) бруска равной длинны, на верхнюю и нижнюю панели. Настал ответственный момент - закрепление задней панели. При этом необходимо выдержать прямой угол между соответствующими панелями, иначе ящик получится кривой.
Передняя панель закрепляется в последнюю очередь, причем, рекомендую не закреплять ее намертво клеем, очень даже возможно, что захочется чего-то изменить... Крепим только шурупами, а для герметизации стыка используем "Поролон для утепления окон и дверей", именно так его называют производители. Продается в рулонах по 9 метров (3 полоски), имеет клейкое основание, этим и удобен. Единственный минус - для наших целей он довольно толстый, и его необходимо разрезать острыми ножницами примерно пополам. Полоски клеим по две на каждый брусок, по краям (фото 5)

Фото 5.
Для прорезания отверстий под динамики можно воспользоваться "балеринкой" (при диаметре менее 150 мм) либо электролобзиком. В крайнем случае, можно насверлить отверстия по кругу, выбить внутреннюю часть и крупным напильником исправить огрехи, но потребуется много времени и сил. Динамик крепится снаружи при помощи винтов (М5х30) и так называемых \"вбиваемых\" гаек (фото 4). При их отсутствии можно изготовить аналог: из стального листа толщиной от 2 мм нарезаем полоски размером приблизительно 10х25 мм, сверлим по краям два отверстия, в одном из них нарезаем нужную резьбу (для 15 дюймового динамика достаточно М5), второе используем для крепления шурупом к панели (естественно, с тыльной стороны, в итоге получается "солнышко" .
Когда ящик собран, приступаем к прорезанию отверстий под терминалы и ручки. Терминал располагаем в центре задней панели.
Для определения места установки ручек необходим один эксперимент: устанавливаем динамик на его законное место, закрепляем. Определяем центр масс АС, для чего кладем на ровную поверхность отрезок трубы, прута или уголка (рукоятка швабры тоже пойдет), ставим сверху ящик (поперечная ось ящика и продольная ось трубы должны быть параллельными ) и добиваемся равновесия, отмечаем на боковой панели точку касания, проводим через нее вертикальную ось ручки. Она не будет совпадать с вертикальной геометрической осью боковой панели, поскольку динамик имеет значительный вес. Высота установки ручек должна обеспечивать удобство транспортировки: несущий не должен изгибать руку в локте, что возможно при очень высоком размещении ручки, а корпус не должен цепляться за невысокие препятствия (в противоположном случае). Расстояние от дна АС до пола при переноске должно составлять 30-40 см.
Итак, места установки динамика, терминала, ручек определены, теперь можно приступать к установке распорок (в качестве которых выступает брус 25х50) между противоположными стенками. Желательно разместить распорки так, чтобы их можно было соединить между собой (непосредственно, либо с помощью отрезка металлического уголка), это придаст корпусу дополнительную жесткость. Они должны примыкать к поверхностям панелей как можно ближе к центру, где амплитуда колебаний наибольшая. Тут и возникает проблема, поскольку эти центры, оказывается, уже заняты: на передней панели - динамиком, на боковых - ручками, увы, их "подвинуть" нельзя. Именно поэтому распорки устанавливаются в последнюю очередь и \"по месту\". Не смею ничего утверждать насчет количество распорок, считаю, что достаточно установить 3 распорки, связав таким образом все противоположные стенки.

Фото 6.
Если динамиков более одного, или корпус вытянутый, то количество распорок между передней и задней, а также боковыми стенками следует увеличить. При этом необходимо "связать" области установки самых тяжелых динамиков.
Теперь устанавливаем фазоинвертор. Желательно найти в магазинах готовую трубу ФИ (которая с красивым фланцем для установки , это очень поубавит проблем. Как вариант, можно использовать пластиковую канализационную трубу, обойдется значительно дешевле, но из-за отсутствия фланца нужно будет помудрить с ее закреплением. В данной конструкции сам ящик является частью трубы (прямоугольного сечения, естественно). Высота определяется высотой брусков, соединяющих нижнюю и боковые панели, ширина - расстоянием между брусками. Остается только добавить верхнюю часть трубы, использовав ту же самую ДСП. Для этого вырезаем из плиты прямоугольник, который должен ложится на указанные бруски и примыкать к передней панели (фото 7). Чтобы она действительно примыкала, необходимо в ней сделать вырезы под вертикальные бруски боковых панелей. Закрепляется эта часть трубы шурупами к брускам и к передней панели, уплотняем оставшимся поролоном на липкой основе, либо пластилином. Замечу, что ФИ нужно будет настраивать, поэтому крепим не намертво. Также следует учесть, что в длину полученной трубы входит и толщина передней панели.
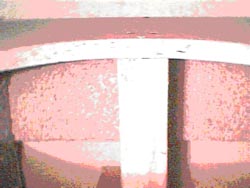
Фото 7.
Внешняя отделка. В данном случае используем для отделки карпет. Сначала подготавливаем ящик. Заокругливаем все острые грани ящика, для чего можно использовать напильник с крупной насечкой (сразу скажу, что занятие это малоприятное и очень трудоемкое). Этим достигаются следующее: ворс карпета не торчит на углах и красиво ложиться, сами углы не выкрашиваются при ударах и становятся менее травмоопасными. Радиус округления определяется используемыми угловыми набойками - они должны плотно примыкать к панелям. Как правило, металлические набойки требуют значительно меньший радиус округления.
Когда весь этот кошмар позади, снимаем установленные ручки, терминалы, набойки (их обязательно следует устанавливать в "черновом" варианте, до отделки карпетом, иначе потом нелегко будет точно сверлить отверстия под шурупы; при сверлении отверстий под крепеж набоек следует внести поправку на толщину карпета) тщательно выметаем опилки из корпуса. Покрываем внешние поверхности любым качественным лаком в один-два слоя (зависит от плотности ДСП, поверхность после высыхания лака должна быть шероховатой; как правило, достаточно одного \"щедрого\" слоя), особенно хорошо пропитываем торцы - наиболее уязвимое место. Сушим.
Кроим карпет. Одним из удачных вариантов раскроя считаю следующий: верхняя, нижняя и боковые панели окутываются одним длинным куском, стык на нижней панели. Задняя панель, торцы и \"внутренняя\" часть (до стыка с передней) боковых панелей оклеивается этим же куском. Сзади получается стык наподобие конверта (фото 8).

Фото 8.
Таким образом, необходимо отрезать кусок размером (2 высоты корпуса + 2 ширины + припуск)х(глубина корпуса + толщина ДСП +глубина посадки передней панели + 0,5 ширины корпуса + припуск). Передняя панель оклеивается в последнюю очередь, отдельным куском, можно даже несколькими, например, из остатков (для справки - ширина рулона составляет 1,8 м, но следует уточнить при покупке).
Для резки и притачивания по месту можно использовать большой канцелярский нож, но лучше всего, использовать нож с широким тонким изогнутым лезвием (наподобие садового). Технология оклейки такова: обворачиваем корпус карпетом, как указано выше, убеждаемся, что его всюду хватает, закрепляем в нескольких местах (например, прищепками за боковую панель со стороны динамика). Не спешите кроить углы и пр., все делается "по месту". Переворачиваем обернутый корпус на бок, аккуратно освобождаем от карпета боковую сторону и начинаем клеить именно с нее. Несколько слов о клеях. Использовал "N88", в банке 0,8 литра, стоимость порядка 2-3 долларов, вполне хватает на три столитровых ящика. Есть специальные клеи для подобных покрытий в аэрозольной упаковке, насколько мне известно - достаточно дороги.
Итак, быстро наносим клей на указанную выше боковую панель корпуса, аккуратно кладем карпет, начиная со стороны верхней панели, хорошенько разглаживаем сначала руками, потом, окончательно и с хорошим усилием, горячим утюгом (температура его должна быть достаточно высокой, чтобы быстро прогревать карпет, точнее, клей под ним, но не плавить волокна; проконсультируйтесь у жены, девушки, мамы. Не следует увлекаться обильным нанесением клея, иначе он просочиться сквозь карпет наружу, склеит волокна и образует пятно, которое практически невозможно удалить. Особенно опасно налить много клея на торцы, где усилие от утюга значительно выше. Время сушки, в зависимости от площади - примерно 5-15 минут.
Предпочтительная последовательность: боковая панель, примыкающая к ней часть нижней, верхняя, боковая, оставшаяся половина нижней. Далее клеим заднюю панель, тут требуется внимание и точность, поскольку склейка производиться "в стык". Чтобы получить ровные и красивые стыки, необходимо отрезать с запасом (около 1 см) и приклеить одну стыкуемую часть, накрыть ее второй, и под металлическую линейку пройтись острым ножом по желаемой линии стыка. После этого убираем отрезанные куски и клеим встык. Доклеиваем оставшиеся участки со стороны передней панели и ее саму, сушим в теплом помещении в течении суток.
Сборка. Спустя указанное время острым ножом вырезаем в карпете отверстия под динамики, ручки, терминалы, трубы ФИ, устанавливаем все, кроме динамика. Для герметизации, при необходимости, используем поролон, резину из автокамер, пластилин и пр.
Наступает завершающий этап - организация звуковибропоглощения и настройка ФИ. Не буду распространятся насчет материалов и особенностях их применения, поскольку данной теме посвящено немало страниц как в печатных изданиях, так и в Инете (например, Р.М. Терещук, К.М. Терещук, С.А. Седов. Полупроводниковые приемно-усилительные устройства. Киев, "Наукова думка", 1989, http://igdrassil.narod.ru/audio/tips/pppsu89/spr_pppsu89.html. Там же можно найти более раннее издание, не менее интересное, читайте начиная отсюда http://igdrassil.narod.ru/audio/tips/pppsu/g9-as/544-559.djvu). Посоветую искать материалы в автомагазинах (рынках). Так, очень полезной будет \"автомобильная шумоизоляция\" - ватин на битумной основе (теоретически, должен обеспечить и виброизоляцию и шумоизоляцию). Хорошо клеится, не дорог, около 7 долларов за полотно 1,7х3 м., но будьте внимательны при покупке, оказывается, разные производители делают ее по разному: одни с толстым слоем битума, другие - с напылением (по другому назвать трудно).
Результат трудов на фото 9, 10. На фото 11 (и фото 8, 12) представлена моя первая работа, двухполосная АС на основе 12 дюймового НЧ-СЧ динамика, и рупорного дюймового ВЧ. В процессе ее создания участвовал Илья Галеев, за что я ему безмерно благодарен.

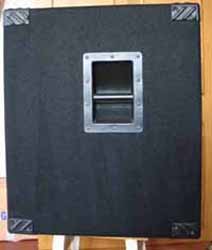
Фото 9. Фото 10.
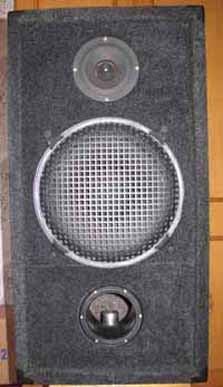
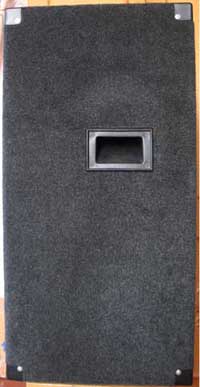
Фото 11. Фото 12.
А так выглядит комплект в боевом положении:
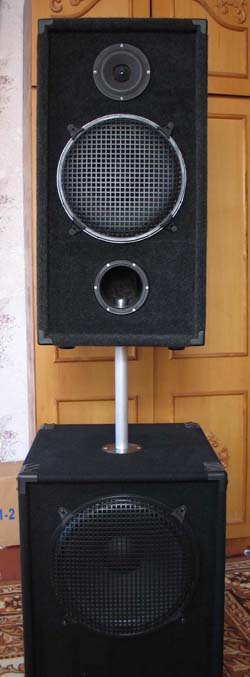
Фото 13.
Об электрической части. Профессиональные АС имеют отключаемый кабель, для соединения используются разъемы типа SPEAKON, JACK 6,3 mm, иногда пружинные, винтовые клеммы. Как правило, терминал имеет два типа разъемов, например, как в нашем случае (фото 14, 15):


Фото 14. Фото 15.
Такая универсальность также очень выручает, когда соединительный кабель забыли либо испортили, повреждены разъемы, что бывает нередко в \"туровой\" практике. С этой точки зрения, наилучшими считаю пружинные (винтовые) клеммы, поскольку соединителем может служить подходящий кусок провода, зачищенный зубами J. Замечу, что именно такое клеммы используются в профессиональных динамиках, что позволяет быстро их демонтировать. В качестве внутренней проводки следует использовать кабель, специально предназначенный для соединения АС, он достаточно мягок, не боится частых изгибов (состоит из значительно большего количества жил при том же сечении, чем силовые кабели). Сечение проводника должно соответствовать передаваемой по нему мощности, как правило, определяется диаметром отверстия в клемме динамика. Длинна кабеля должна обеспечивать удобство демонтажа динамика, по возможности, следует закрепить кабель. Не допускайте, чтобы кабель проходил над динамиком, он может попасть на диффузор и повредить его.
Если в АС применяются фильтры, следует особое внимание обратить на надежность закрепления его элементов, все резьбовые соединения должны быть залиты лаком во избежание самопроизвольного откручивания. Электрические соединения элементов должны иметь минимальную длину и надежную пайку. Кардинальное решение - заливание собранного и настроенного фильтра компаундом.
На данный момент все. Возможно, будут дополнения и изменения. Буду рад советам и конструктивной критике.
Полезные ссылки (заранее прошу прощения, некоторые из них явно коммерческого направления):
http://dmitriks.narod.ru/books/books.html - Хорошая библиотека.
http://members.tripod.com/~sakevich/ - Профессиональные усилители и АС.
http://shuttle-st.narod.ru/akust.htm - Книги.
http://www.avc.ru - Примеры конструкторов АС, каталог всего необходимого для постройки.
http://www.newton-lab.ru - Немного теории и практики.
Комментарии
Здесь никто ничего не написал. Вы можете быть первым.